3D printers just got a big, eco-friendly upgrade (in the lab)
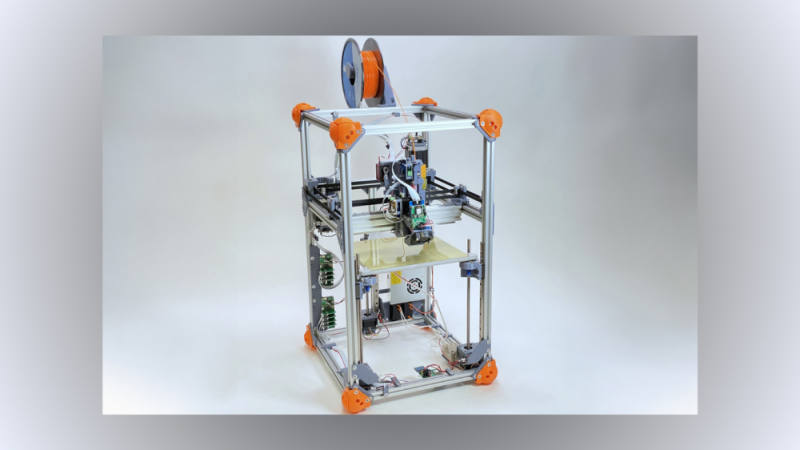
A team of international researchers have developed an adaptation to potentially help with 3D printing’s polymer problem.
For quick prototyping jobs, designers often turn to fused filament fabrication (FFF) 3D printers. In these machines, molten polymers are layered atop one another using a heated nozzle. This process is underpinned by what’s known as slicer software, which informs the device of all the little details like temperature, speed, and flow necessary to make a specific desired product, instead of an amorphous blob of congealed goo. But a slicer only works for a reliably uniform material—that wouldn’t be too much of a problem, except most of those materials are often unrecyclable plastics.
But thanks to engineers collaborating between MIT’s Center for Bits and Atoms (CBA), the US National Institute of Standards and Technology (NIST), and the National Center for Scientific Research in Greece, a little computational fine-tuning can now allow an off-the-shelf device to analyze, adjust, and successfully utilize previously unrecognizable printing materials in real-time to create more eco-friendly products.
3D printers often rely on unsustainable materials, but you can’t simply swap out those polymers for potentially more sustainable alternatives. Unlike artificial polymers, eco-friendly options contain a mix of various ingredients that result in widely varying physical properties. Plant-based polymers, for example, can change based on what’s available season-to-season, while recyclable resins fluctuate depending on its source materials. Those can still be used, but a device’s software parameters would need tweaking for each and every batch. And considering how a 3D printer’s programming usually contains as many as 100 adjustable parameters, this makes recyclable workarounds a difficult sell.
In a new study published in Integrating Materials and Manufacturing Innovation, engineers detailed a newly designed mathematical function that allows off-the-shelf 3D-printer’s extruder software to use multiple materials—including bio-based polymers, plant-derived resins, or other recyclables.
First, researchers took a 3D printer built to provide data feedback while it is working, then outfitted it with three new tools to measure various factors such as pressure, filament thickness, and speed. Once installed, the team created a 20-minute test during which those instruments measured varying flow rates as well as their associated temperatures and pressures. After some trial-and-error, engineers realized the best approach to this was to set the hottest temperature possible for a 3D printer’s nozzle, also known as a “hotend,” for obvious reasons. In this case, the hotend’s maximum temperature lived up to the name—290 degrees Celsius, or about 554 Fahrenheit. They then set it to extrude filament at a steady rate, turned off the heater, and let it run.
“It was really difficult to figure out how to make that test work. Trying to find the limits of the extruder means that you are going to break the extruder pretty often while you are testing it,” CBA graduate student and study first author Jake Read said in a statement on Monday. “The notion of turning the heater off and just passively taking measurements was the ‘aha’ moment.”
Read and their collaborators then entered the information gleaned from their test into a new mathematical function that automatically computed workable printing parameters and machine settings depending on material. Once those were available, the team simply entered the parameters into the 3D printer software and let it run normally.
To test their system, researchers used six different materials to 3D print a small toy tugboat. Even including eco-friendly options derived from algae, wood, and sustainable polylactic acid, engineers reported no “failures of any kind” in their small model vessels—although from an aesthetically standpoint, the wood and algae resins did make for rather stringy-looking final products.
But while the new alterations may not yet offer a “complete reckoning with all of the phenomenology and modeling associated with FFF printing,” the team believes the system shows that “even simple methods in combination with instrumented hardware and workflows that connect machines to slicers can have promising results.”
Next up, researchers hope to expand on their computational modeling efforts, as well as design a way so testing parameters can automatically apply to a 3D printer instead of requiring manual entry. In the meantime, they have made their mechanical and circuit designs, as well as firmware, framework, and experiment source codes available online for others to try for themselves.