Tribologists Discover Self-Lubricating and Self-Healing Tribofilm That Could Revolutionize Lubrication
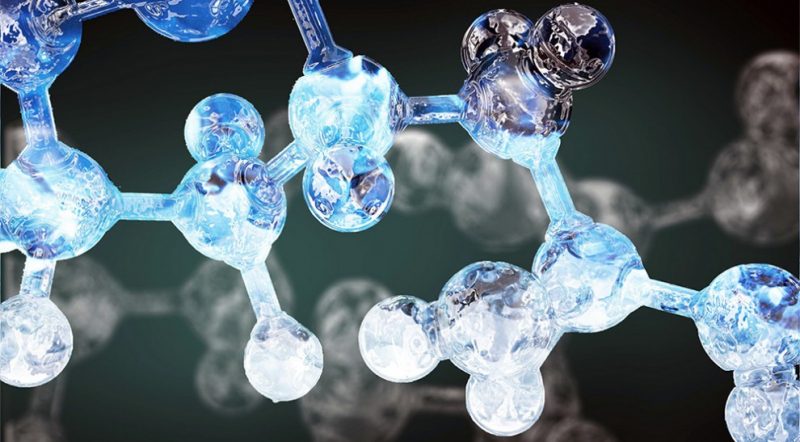
Tribologists and computation materials scientists at the United States Department of Energy’s Argonne National Laboratory has discovered an ultra-durable, self-lubricating tribofilm. This film forms between moving surfaces and was first reported last week in Nature Journal. It holds the potential of profound implications for the efficiency and durability of future engines and other moving parts that can be made to develop self-healing, diamond-like carbon tribofilms.
Ali Erdemir, Argonne Distinguished Fellow and leader of the team said this is a very unique discovery, and one that was a little unexpected. We have developed many types of diamond-like carbon coatings of our own, but we’ve never found one that generates itself by breaking down the molecules of the lubricating oil and can actually regenerate the tribofilm as it is worn away.
The phenomenon was first discovered a few years ago by Erdemir and his colleague Osman Levent Eryilmaz in the Tribology and Thermal-Mechanics Department in Argonne’s Center for Transportation Research. It took a lot of theoretical insight that was enhanced by the massive computing resources available at Argonne to fully comprehend what was happening on a molecular level throughout the experiments. The theoretical understanding was built by lead theoretical researcher Subramanian Sankaranarayanan and postdoctoral researcher Badri Narayanan from the Center for Nanoscale Materials. The computing power was created by the Argonne Leadership Computing Facility and the National Energy Research Scientific Computer Center at Lawrence Berkeley National Laboratory.
The original discovery took place when Erdemir and Eryilmaz wanted to see what would happen when they coated a small steel ring with a catalytically active nanocoating and then added high pressure and heat using base oil without the complex additives that are present in most modern lubricants. When an endurance test was done on the ring, they were expecting to not see rust and surface damage. They thought they would find a ring completely intact with an odd blackish deposit where the contact area had been.
Eryilmaz says this test creates extreme contact pressure and temperatures which are supposed to cause the ring to wear and eventually completely seize. However, this ring didn’t significantly wear and this blackish deposit was visible. We said, ‘Material is strange. Maybe this is what is causing this unusual effect.’”
Using high-powered optical and laser Raman microscopes, the team looked at the deposit and experimentalists soon realized that the deposit was a tribofilm of diamond-like carbon which was very similar to several other DLCs that had previously been developed at Argonne in the past. However, this one worked much better than the previous ones had. Test showed the DLC tribofilm reduced friction by anywhere from 25 to 40 percent and the actual wear was reduced by immeasurable amounts.
More testing was done by postdoctoral researcher Giovanni Ramierz that showed multiple types of catalytic coatings can yield DLC tribofilm. The experiments showed the coatings actually interact directly with the oil molecules in order to create the DLC film which is what adheres to the metal surfaces. When the tribofilm is worn down the catalyst in the coating is then re-exposed to the oil which causes the catalysis to start over and to develop brand new layers of tribofilm. The process is known as self-regulating which keeps the film at a thickness that remains consistent. The scientists discovered that the film was developing spontaneously between the sliding surfaces and was replenishing on its own. The only thing they did not understand was why this was happening or how.
In order to come up with a theoretical understanding of exactly what the tribology team was seeing during their testing, they worked with Sankaranarayanan and Narayanan who had previously used the immense computing power of ALCF’s 10-petaflop supercomputer known as Mira. They ran large-scale simulations in order to get a better understanding as to what was happening on an atomic level and realized that the catalyst metals in the nanocomposite coatings were stripping hydrogen atoms from the hydrocarbon chains of the lubricating oil. They were then breaking down the chains into even smaller segments. These smaller chains came together under pressure and created the highly durable DLC tribofilm.
Sankaranarayanan says this is an example of catalysis under extreme conditions created by friction. It is opening up a new field where you are merging catalysis and tribology, which has never been done before. This new field of tribocatalysis has potential to change the way we look at lubrication.
Theorists dug deeper into the origins of the catalytic activity to gain a better understanding of how catalysis operates under the extreme heat and pressure within engines. By better understanding how this works they were able to predict which catalysts would work and which would lead to the most advantageous tribofilms.
Narayanan says interestingly, we found several metals or composites that we didn’t think would be catalytically active, but under these circumstances, they performed quite well. This opens up new pathways for scientists to use extreme conditions in order to enhance catalytic activity.
The implications created by the new tribofilm as far as efficiency and reliability of engines are massive. Manufacturers already use a wide range of different types of coating for metal parts in engines as well as a lot of other applications. The problem remains that these particular coatings are costly and very hard to apply, and once they are in use, they only last until the coating wears off. The new catalyst allows the tribofilm to be continually renewed while operation is still taking place.
The tribofilm develops in the presence of base oil so it allows manufacturers to reduce and maybe even completely get rid of some of the modern anti-friction and anti-wear additives that are currently used within oil. These additives have been known to not only decrease the efficiency of vehicle catalytic converters, but are also harmful to the environment due to their heavy metal content.